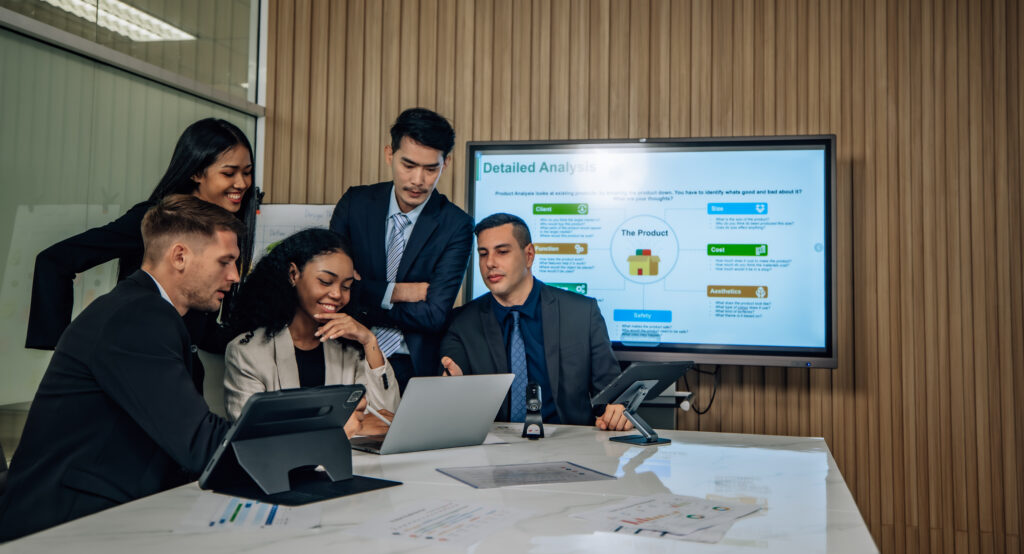
S&OP Pro – A Discrete Manufacturing ERP
To address the challenges faced by sales teams and shop floor professionals in areas like production planning, material planning, capacity planning, and data analysis, we’ve developed Sales and Operation Planning Pro [S&OP Pro]. This innovative solution supports a variety of manufacturing environments, including MTS, MTO, ATO, ETO, and project-based industries. Packed with world-class features, S&OP Pro offers a competitive edge without breaking the bank. Key features include Sales and Demand forecasting, Purchasing Management, Advanced Pricing, Inventory Management, Master Production Scheduling, Material Requirement Planning, Rough Cut Capacity Planning, Product Costing, and seamless integration with Business Intelligence tools like Microsoft Power BI for data-driven decision-making. Designed specifically for discrete manufacturing, S&OP Pro empowers organizations to optimize their operations and achieve greater efficiency.
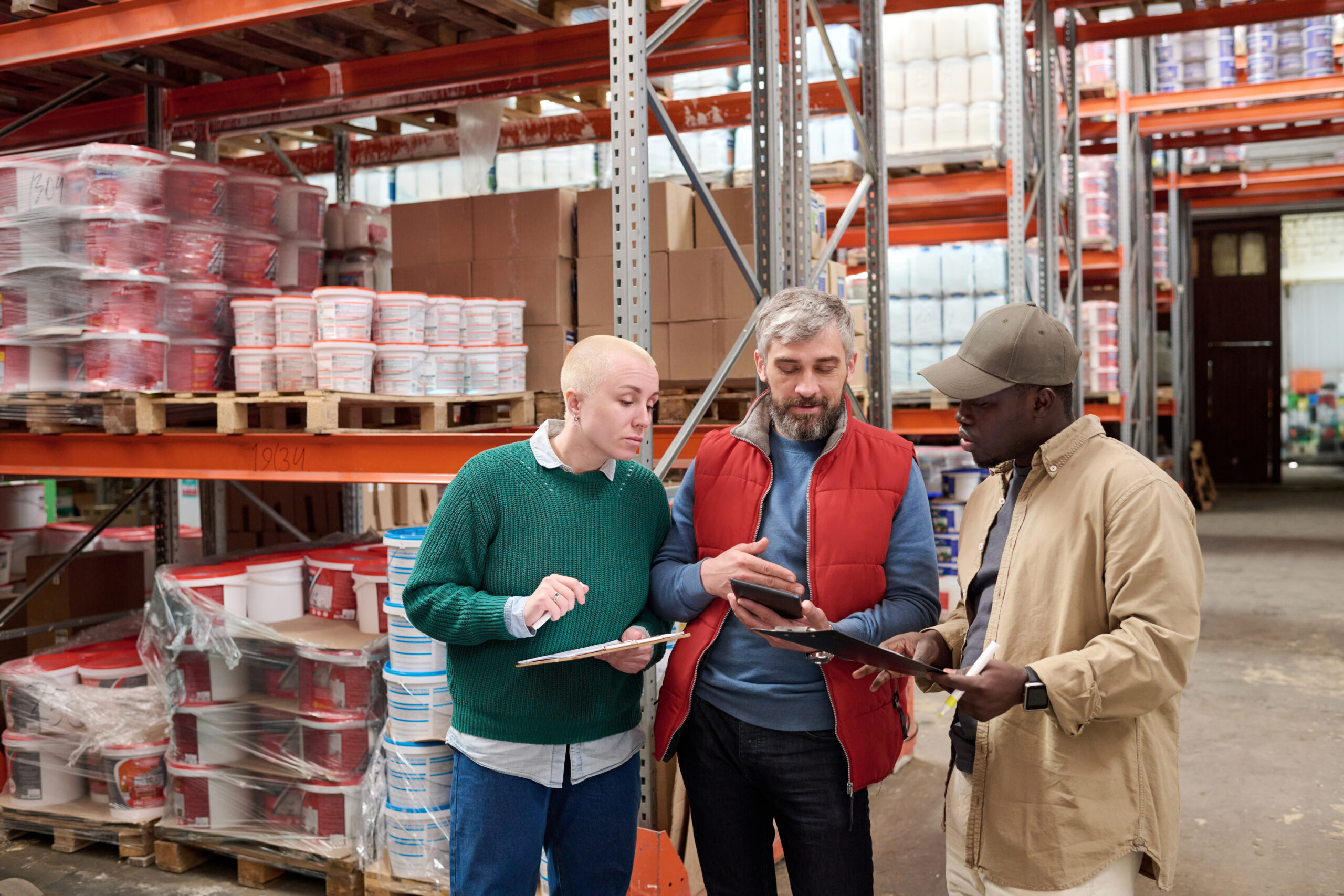
Sales and Distribution
To address the diverse global demand landscape, this module is designed to provide organizations with the following capabilities. Seamlessly integrated with Master Production Scheduling, it enables users to input demand in the form of Firm Demand (Sales Orders), Forecast Demand (at SKU and Customer levels), and Customer Schedules (at SKU level). Flexible shipment confirmation options include One-to-One, One-to-Many, and Many-to-Many relationships. Invoicing is streamlined with support for both One Shipment to One Invoice and Many Shipments to One Invoice. The module accommodates both foreign and domestic currencies and offers seamless integration with Accounts Receivable (AR) systems, including popular local financial software like Tally.
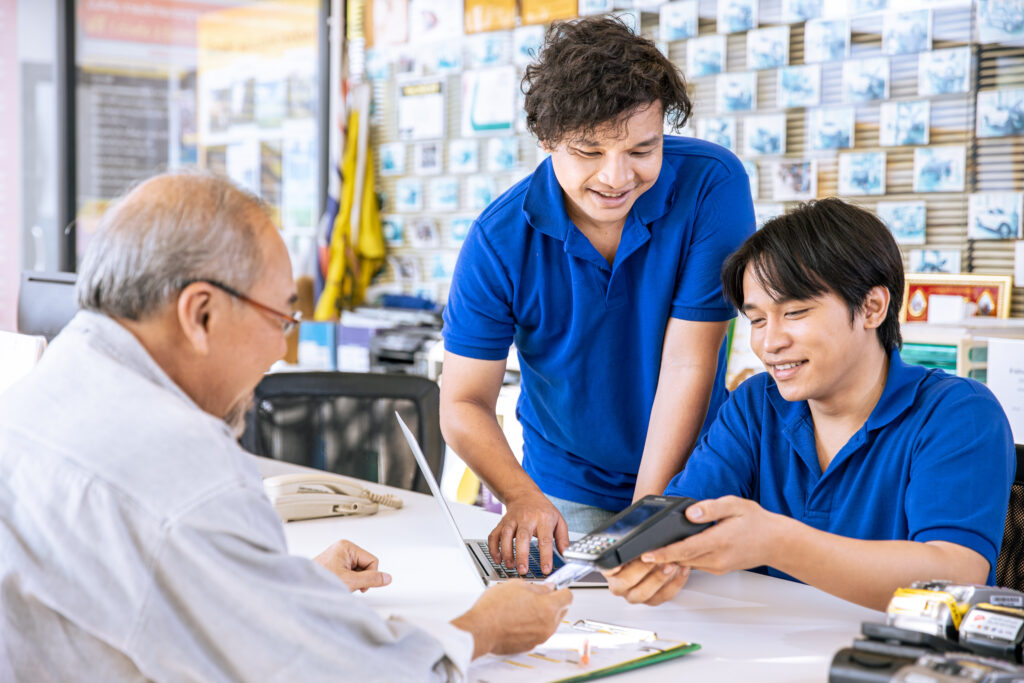
Purchasing Management
This module provides comprehensive procurement functionality, seamlessly integrated with Production Planning and Material Requirement Planning. Key features include:
- Purchase Requisition Entry: Create and manage purchase requisitions.
- Purchase Order Generation: Convert purchase requisitions into purchase orders.
- Goods Receipt Note (GRN) Processing: Record and manage goods receipts against open purchase orders.
- Accounts Payable Integration: Integrate GRNs with Accounts Payable systems for seamless financial management, including popular local software like Tally.
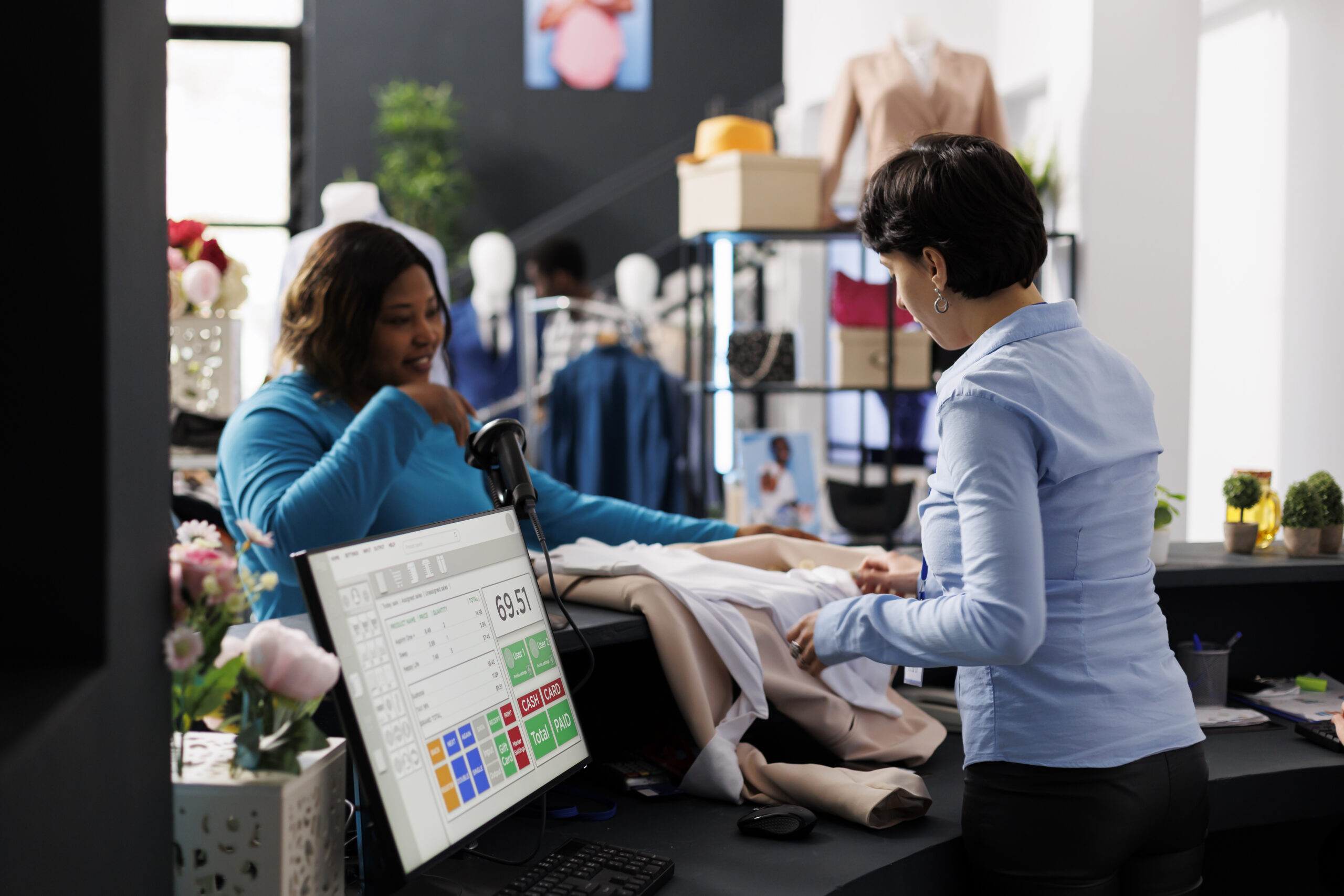
Advanced Pricing
To address the evolving global landscape, including government policy changes and varying customer demands, we have introduced a flexible pricing feature. This feature enables organizations to define pricing at two levels: Material Sales Price at the Plant Level and/or Customer/Supplier Pricing at the Material Level. This granular approach allows for precise pricing control at the individual material level, using the following schema:
- Slab Pricing: Define pricing based on quantity slabs (e.g., pricing for 1-500 units, 501-9999999 units).
- Additional Charges, Discounts, and Taxes: For each slab, apply multiple additional charges, discounts, and taxes.
By attaching specific pricing schemas to individual line items on Sales Orders and Purchase Orders, businesses can ensure accurate and compliant pricing in diverse market conditions.
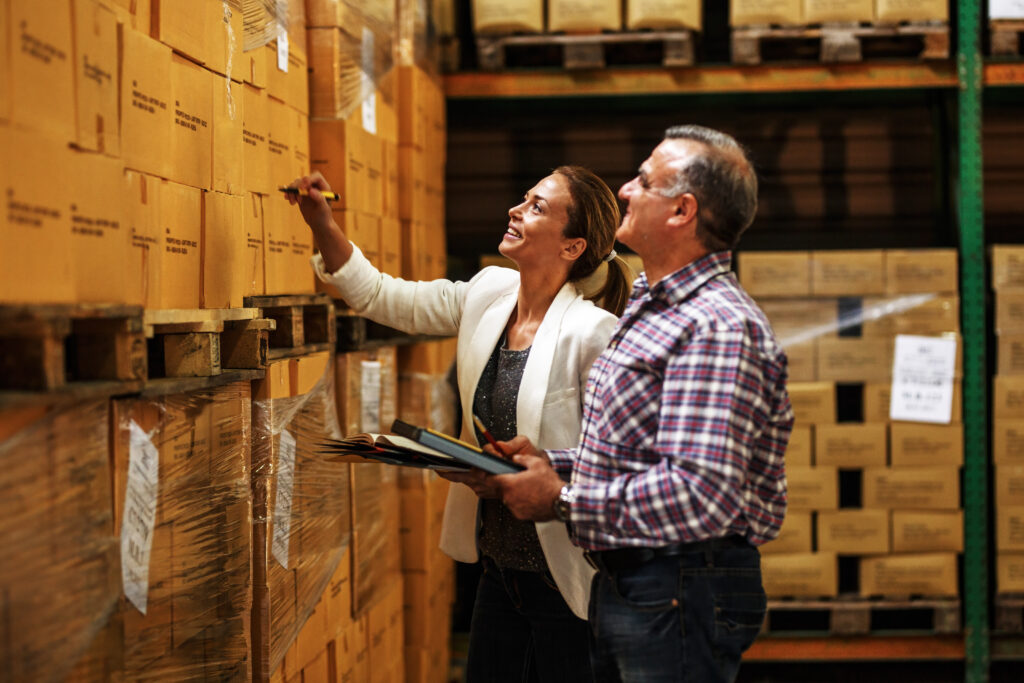
Inventory Management
This module offers world-class inventory management capabilities, drawing on global best practices. You can categorize inventory into four distinct types: Blocked Stock, QC Stock, Released Stock, and Rejected Stock. Additionally, the system allows you to maintain inventory at five organizational levels: Company Level, Plant Level, Location Level, Aisle Level, and BIN Level. Key features of our inventory management module include:
- Inventory Adjustments: Easily adjust inventory quantities.
- Inventory Transfers: Efficiently transfer inventory between locations.
- Inventory Reclassifications: Reclassify inventory items based on changing needs.
General Ledger Integration: Seamlessly integrate inventory transactions with your general ledger system, including popular local software like Tally.
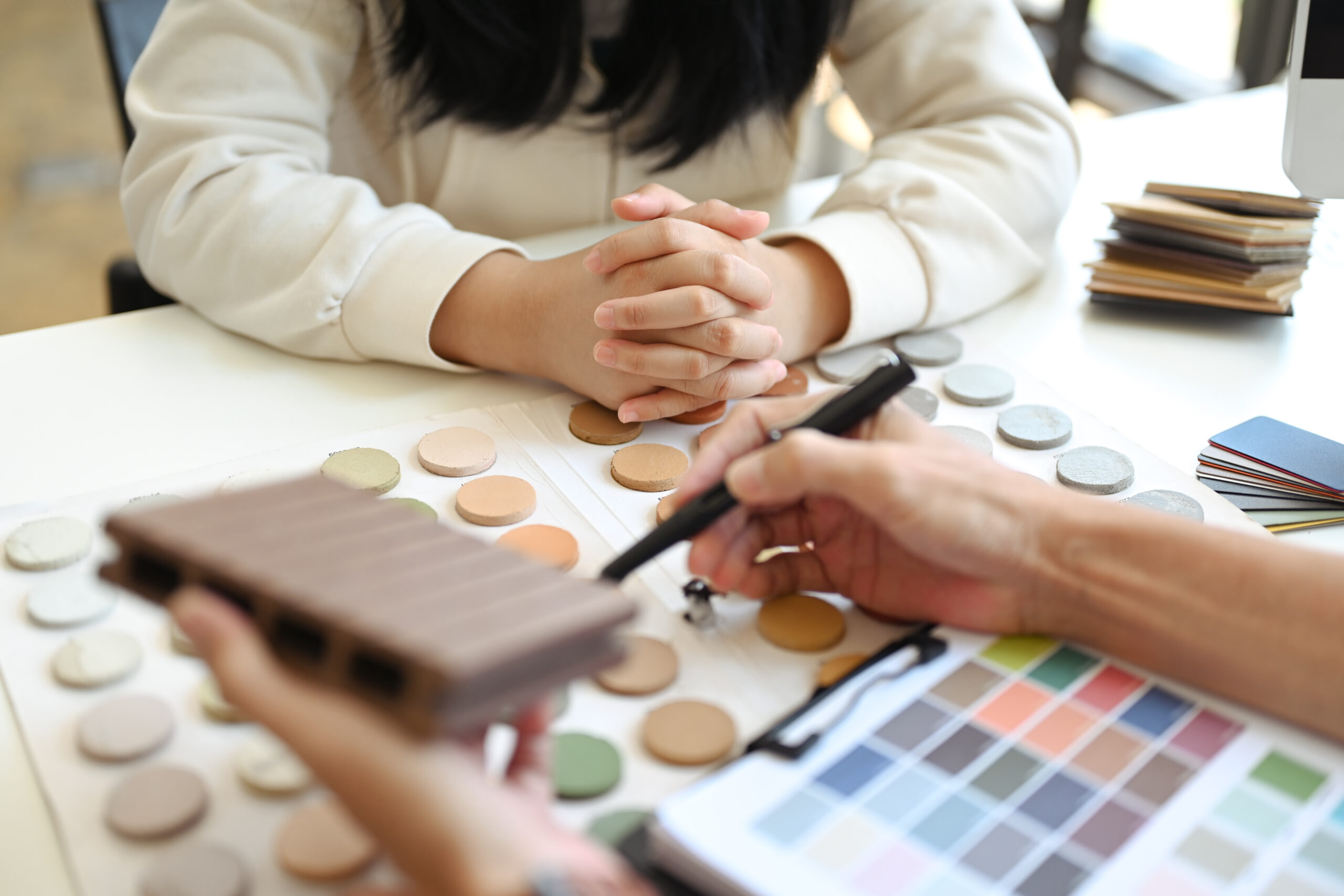
Product Costing
Our product costing module is designed with a global perspective, emphasizing the importance of approximate accuracy over precise error. This unique feature enables organizations to simulate costs using three key components:
- Raw Material Level: Calculate costs based on Standard Bills of Materials.
- Operation Cost: Determine costs associated with product routing.
- Overhead Cost: Allocate overhead costs to each SKU.
This flexible approach allows for multiple cost simulations, ensuring organizations can refine their cost estimates and ultimately freeze costs at the SKU and WIP levels at the Material Plant level until the next revision. Users can simulate costs, review detailed Cost Cards, and perform cost estimations for specific batch sizes.
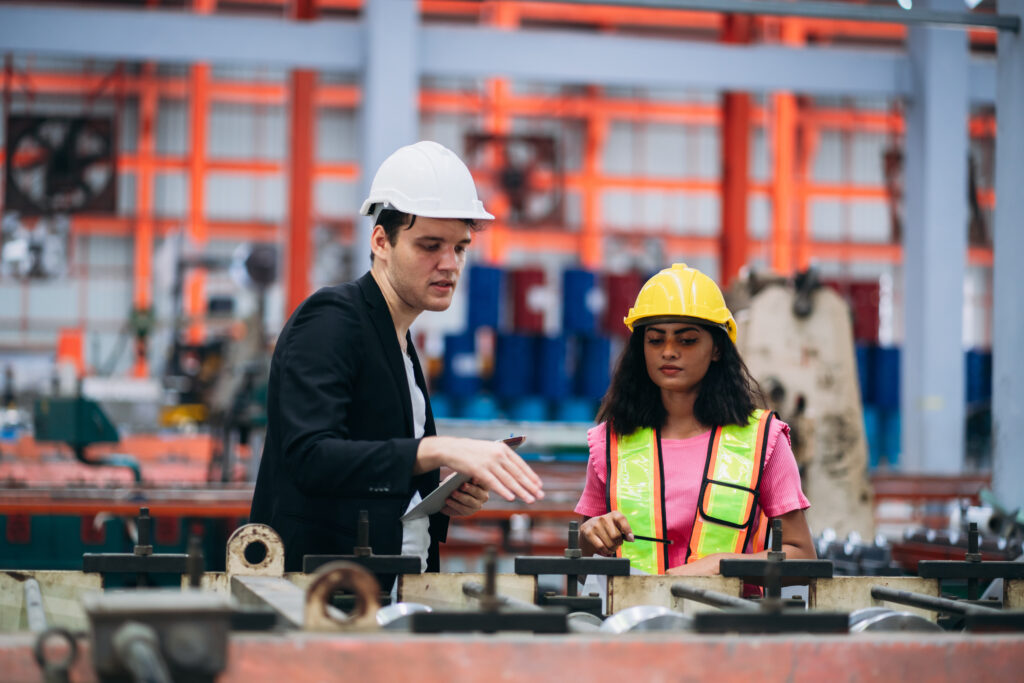
Master Production Scheduling
This module provides comprehensive procurement functionality, seamlessly integrated with Production Planning and Material Requirement Planning. Key features include:
- Purchase Requisition Entry: Create and manage purchase requisitions.
- Purchase Order Generation: Convert purchase requisitions into purchase orders.
- Goods Receipt Note (GRN) Processing: Record and manage goods receipts against open purchase orders.
- Accounts Payable Integration: Integrate GRNs with Accounts Payable systems for seamless financial management, including popular local software like Tally.
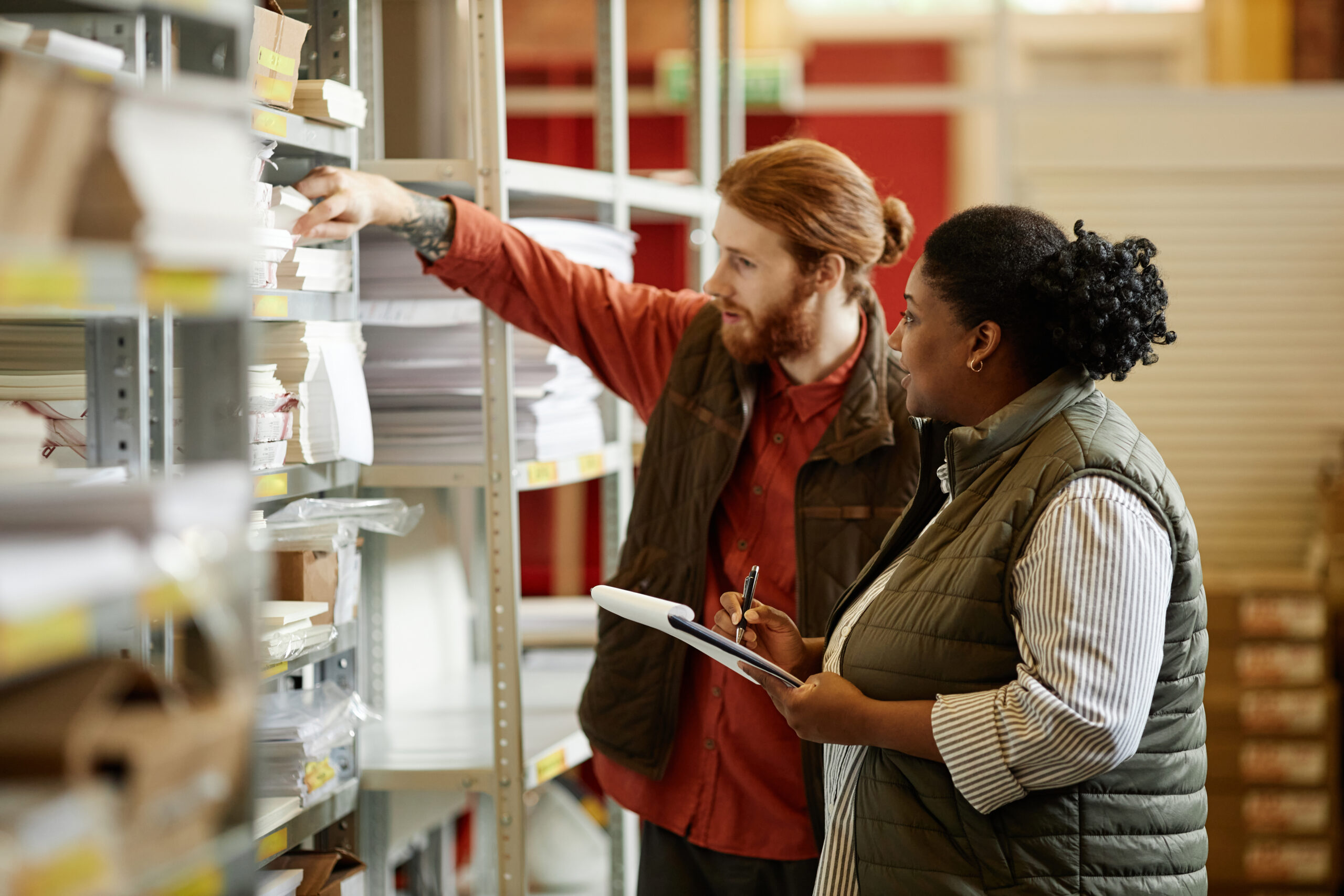
Material Requirement Planning
This module enables you to accurately calculate material requirements based on your Master Production Schedule, while also considering independent forecasts at the Raw Material level. This comprehensive approach ensures that your material planning aligns with both your production plans and market demand.
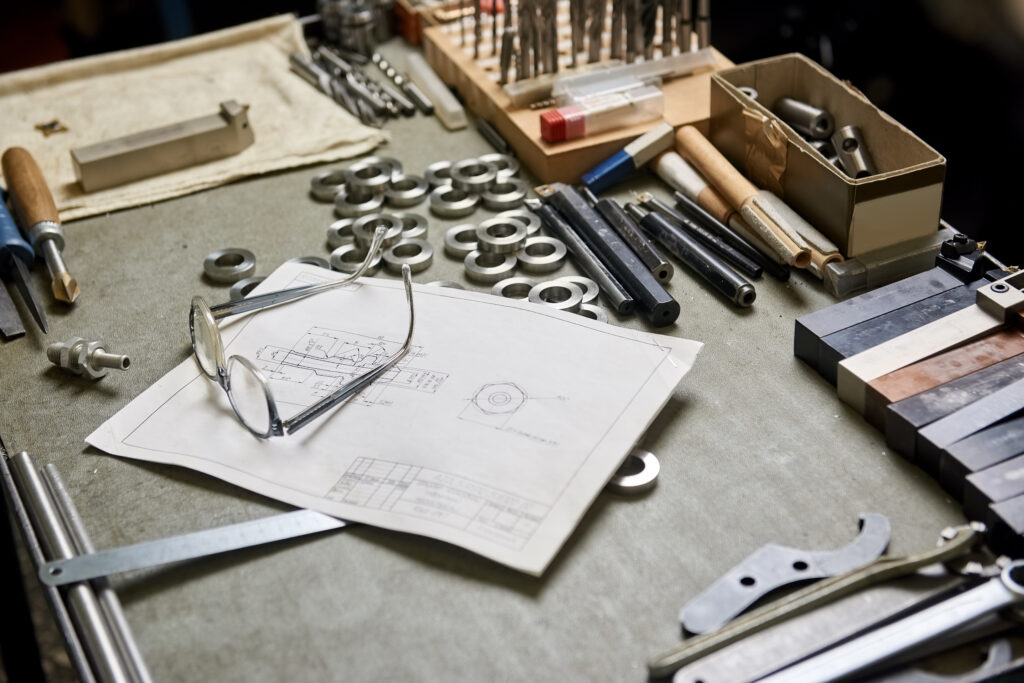
MPS/MRP Workbench
This dedicated workspace is designed for production and procurement planners to review and finalize proposals generated by the latest Master Production Schedule (MPS) and Material Requirement Planning (MRP) runs. Planners can use this workbench to assess proposals based on exception messages, such as:
- Lead Time Violations: Identify materials with insufficient lead times.
- Expedite/De-Expedite Materials: Determine materials requiring expedited or de-expedited processing.
- Planning Time Fence (PTF)/Demand Time Fence (DTF) Violations: Assess materials that violate planning or demand time fence constraints.
By analyzing these exceptions, planners can make informed decisions to convert proposals into optimal Production Orders and Purchase Orders.